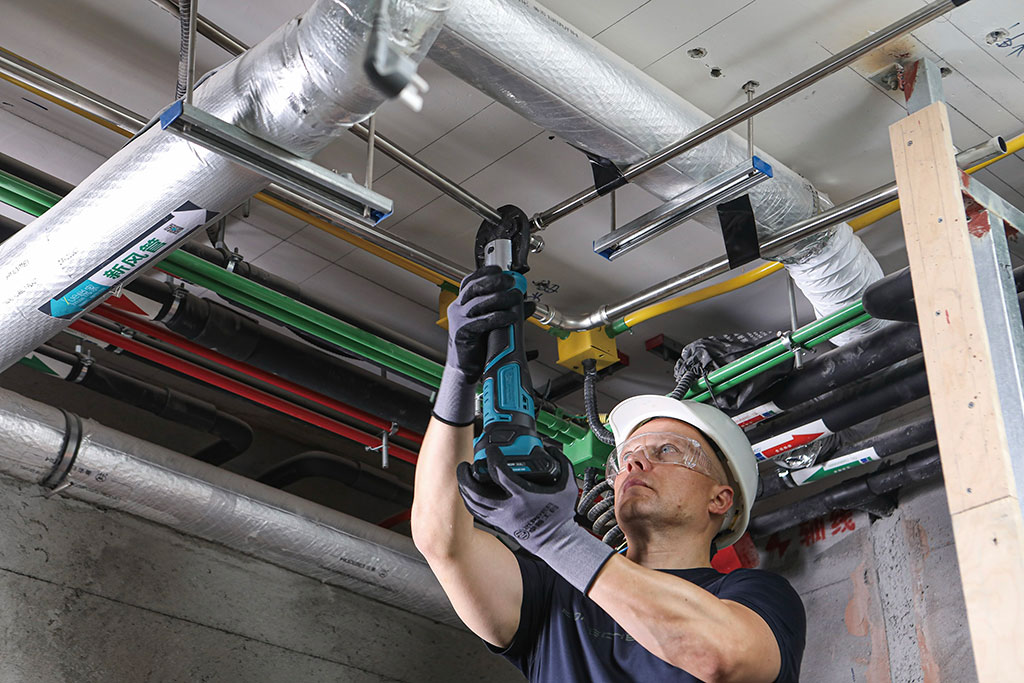
When it comes to choosing the right press tool for plumbing, heating, or HVAC work, the age-old hydraulic system has a strong reputation. But as the industry evolves, direct-drive press tools are emerging as a smarter, more efficient solution for modern installers. With this in mind the new direct-drive tool Z-PRESS tool by Zupper is now available from stockists and supports the other tools in the range, PZ-1930 and PZ-1550.
So, what exactly is the difference—and why should you consider going direct-drive?
What Is a Direct-Drive Press Tool?
Unlike traditional hydraulic press tools that rely on a fluid-filled pump to generate pressing force, direct-drive tools use a brushless electric motor and gear system to deliver the power needed to press a fitting. This simplified system removes the hydraulic component altogether.
Key Benefits of Direct-Drive Over Hydraulic Press Tools
- No Hydraulic Fluid – No Leaks, No Hassle
Hydraulic tools require fluid to generate pressing force. Over time, seals can wear and fluid can leak—causing downtime and messy maintenance.
Direct-drive systems eliminate this risk completely, offering a dry, clean operation with fewer potential failure points.
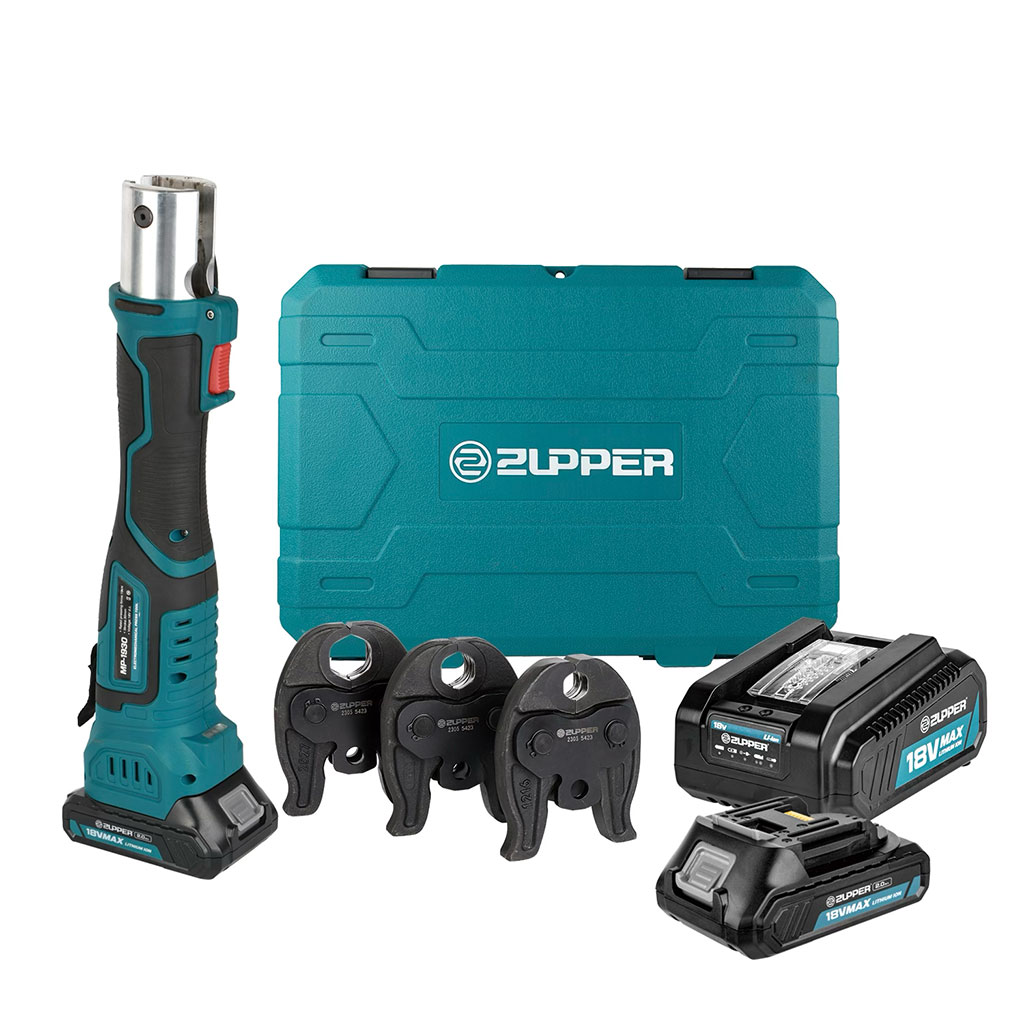
- Lower Maintenance and Longer Service Intervals
With fewer moving parts and no hydraulic circuit, direct-drive tools are inherently simpler.
Fewer seals to replace
No hydraulic oil changes
Less internal wear over time
This means longer service intervals, reduced downtime, and lower lifetime costs. - Faster Cycle Times
Direct-drive tools typically offer faster, smoother press cycles, with no delay while a pump builds pressure.
Installers can move more quickly from joint to joint—especially valuable on large projects where time is money. - Improved Tool Reliability
Hydraulic systems are sensitive to cold, moisture, and dirt, which can affect pump performance.
Direct-drive systems, especially those with sealed brushless motors, perform consistently in tough site conditions and across temperature ranges. - Lighter and More Balanced Design
Without the added weight of a hydraulic pump and fluid reservoir, direct-drive tools can be lighter and better balanced, reducing fatigue during overhead or repetitive work.
Perfect for tight spaces and long days on site. - Cleaner Environmental Footprint
No hydraulic oil = no environmental disposal issues. This makes direct-drive tools more sustainable, especially on eco-conscious construction sites or projects with strict health & safety protocols.
Who Benefits Most?
- Service engineers who work in tight spaces or domestic environments
- Commercial installers who need to press hundreds of joints a day
- Companies looking to reduce tool downtime and maintenance costs
- Sustainable contractors aiming to reduce waste and environmental risks
The Bottom Line
Hydraulic press tools have served the trade well—but direct-drive is quickly becoming the new standard. With faster cycles, less maintenance, and greater reliability, direct-drive press tools are a cleaner, smarter choice for the modern installer.
Whether you’re upgrading your fleet or investing in your first tool, it might be time to leave the hydraulics behind. Z-PRESS by Zupper Tools offers a range of tools including the new MP-1930 direct-drive battery operated hand-tool that has a raft of accessories including various profile jaws, 180º jaws and presses up to 35 mm.